Traditional pin-in-paste processing methods used by printed circuit board (PCB) assemblers are being overtaken by a new hybrid alternative innovation: the True Grip Contact Pin.
From the process to its pros and cons, we’re taking a closer look at the True Grip Pin to give you an overview of why it’s a viable, affordable, and reliable customized alternative.
What Is Pin-in-Paste?
Pin-in-Technology (PiP) is also known as Through-Hole-Reflow (THR) technology has been around for a while, developed in 1985 and used by engineers across industries since then.
Lead-free solder paste is printed into through holes for the electrical contact pins. Through-hole components are assembled on the electronics board.
When the soldering paste melts, the liquid solder is pulled into the through-holes, and they form the solder joint. All the components involved need to withstand high temperatures caused by the high thermal loads on the reflow process.
The THR’s component's ability needs evaluation by an engineer to ensure that they can withstand a reflow temperature of up to 260°C over several seconds.
In addition to these technical specifications, there are benefits and drawbacks to PiP.
The Pros
First, let's take a look at the perks:
- Low cost due to the commonality of the practice, prices of tooling, and possible handling damage
- Achieve adequate hole fill and reliable solder joints
- Use the same Pick-and-Place equipment for both SMT and THR components
- Reduce machine set up time, production turn around, and space
The Cons
The effectiveness of this technology is dependent on the preparation of its components.
If the diameter of the PCB hole is too big, it will need too much solder to fill it up. This makes it difficult to correctly fill the hole with paste when solder paste printing. Additionally, if using a low solder volume, defects may appear in the solder.
Here are a few drawbacks to also keep in mind about Pin-in-Paste technology:
- Mess and loss of solder
- The volume of paste in the through-holes is hard to control
- Traditional pin-through-paste processing disburses conductive material, creating contamination, defects, and scrap
True Grip Contact Pins
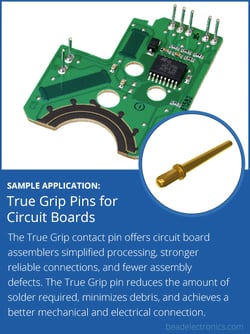
Innovation is the key to success. Leveraging True Grip Pins instead of traditional pin-in-paste processing is cutting-edge because the True Grip Contact Pin is easier to insert by simply applying pressure to the flange, using up to 33% less soldering. Additionally, there's no need to clean THR components at the end of the process.
You only need a tiny amount of solder under the flange to create a reliable and robust joint. The amount of solder required is therefore reduced as is the amount of debris. Assemblers achieve a more effective electrical and mechanical connection. And since you're using less solder, the circuit board is easier to modify. So, if you need to remove parts, you can do so without compromising the integrity of the structure as a whole.
It means there’s no bending, which is something that can happen when using traditional pin-in-paste methods to apply pressure to the pin tip. The True Grip Contact Pins have a consistent pin height.
More and more circuit board assemblers are turning to the True Grip Contact Pin during the design for manufacture (DFM) process. True Grip Contact Pins offer reliable and robust electrical connections. They offer a simplified approach, and fewer defects during the assembly process, alongside power production costs.
What Are True Grip Contact Pins Made From?
They are typically made from the following base metals:
- Brass alloy 26
- Copper alloy 102 and 110
- High-performance copper alloys 194 and 197
- Nickel alloy 201
- Phosphor bronze alloy 510
They can be plated in any of the following:
- Gold
- Nickel
- Palladium
- Silver
- Tin
- ...or tin/lead (not RoHS compliant)
Check out all your plating options in our free whitepaper.
True Grip Contact Pin Design and Advantages
The Bead True Grip Contact Pin is a hybrid through-hole SMT design with more mechanical strength and less electrical resistance. The square through-hole connection firmly engages the PCB.
Simultaneously, the unique flange defines a consistent seating plane and presents a large soldering surface for reliable and robust surface mount processing.
When traditional connector pins are inserted through discs of solder paste, there is a dispersal of conductive material. This can potentially contaminate the PCB, resulting in expensive defects and scrap.
Each True Grip Contact Pin is 100% vision inspected, which guarantees the highest quality electrical contact pins in the industry.
Also, five critical dimensions are checked on each pin before it is wound onto a reel, guaranteeing uniformity and more effective processing.
Pin-in-Paste vs. True Grip Contact Pins: Which Will You Opt For?
PCBs for the automotive, computer, industrial application, and telecom industries need higher quality and more reliable interconnect pins that are economical to buy and easy to process.
We have designed the True Grip Contact Pin to be the most reliable and cost-effective electrical contact pin on the market.
Give your customers a better electrical connection while saving them money. The True Grip Contact Pin has many advantages over the traditional Pin-in-Paste methods we've outlined.
To find out more about how you can use Bead’s True Grip Contact Pins for your next project, get in touch today. We love collaborating!
Complete and submit your design specifications. Our engineering tooling team will build what you need. Speak soon!
About Bead Electronics
Bead Electronics, is a global manufacturer of electronic connectors and contact pins and has been manufacturing in Connecticut for over 100 years. The award-winning company carries over 500 patents and is best known for inventing its manufacturing process called swaging. This process is a high-speed, virtually scrap-less, cold-forming process capable of producing a wide size range of metal electronic components that are consistent and cost-effective. The family-owned business is led by its fifth generation. Click here to speak to a connector pin specialist today.