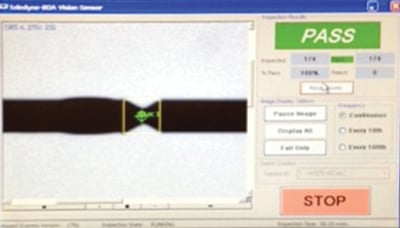
Several more Vision Inspection Systems have been mounted and are running on the factory floor this month. Using an automated solution for inspection allows us to verify the diameter, thickness, and length of each and every connector pin produced, as opposed to just a handful done manually using micrometers.
We're also able to check dimensional accuracy on parts against geometrical tolerances.
The manual method, although reliable, yields only about 100 or so inspected pieces per day, a very small percentage of the connector pins we produce daily. Moreover, if a customer received any parts out of tolerance, the whole lot could be rejected, which could be as many as 2 million connector pins.
In addition to flaw detection, benefits of automated vision inspection systems (VIS) are:
- Product traceability down to the day, hour and minute of production
- More insight into process variables such as tool wear so we can proactively schedule tool changes
- Reduction in costly and inconvenient product returns
Vision system inspection has given us more insight into our process and has helped us in setting a successful and preventative maintenance program on every machine. Our customers can have complete confidence in every single interconnect pin we produce.
About Bead Electronics
Bead Electronics, is a global manufacturer of electronic connector pins and has been manufacturing in Connecticut for over 100 years. The award-winning company carries over 500 patents and is best known for inventing its manufacturing process called swaging. This process is a high-speed, virtually scrap-less, cold-forming process capable of producing a wide size range of metal electronic components that are consistent and cost-effective. The family-owned business is led by its fifth generation. Click here to speak to a connector pin specialist today.